MYOB has unveiled an impressive array of new features in the 2024.1 Spring Release. This blog will explore the latest enhancements and features for managing your supply chain with MYOB Acumatica.
DRP - Distribution Requirements Planning
Gain the clarity you need to avoid over-ordering or stock shortages with Distribution Requirements Planning (DRP).
Previously, wholesale customers managed inventory without the benefit of smart reminders for lead times and exception messages, often leading to over-ordering, shortages, and increased manual effort.
With the MYOB Acumatica 2024.1 Release, a DRP Dashboard has been introduced to streamline inventory management. DRP is a robust planning tool for distribution businesses, designed to meet demand while maintaining optimal inventory levels within a centralized system. It enhances distribution efficiencies by preventing both stockouts and overstocking. DRP recommends quantities to purchase, produce, or transfer and provides exception messages to alert users, helping to maintain balanced inventory levels.
From the new Inventory Planning Display screen:
- Users can plan across multiple warehouses, raising Transfer Orders as needed (considering transfer lead times between warehouses), or purchase from preferred vendors so that suggested ‘Action Dates’ are backdated sufficiently to ensure goods are delivered by the ‘Promise Date’ for Just-In-Time (JIT) inventory management.
- Users can view the sales orders driving demand, with the ability to drill down to the source document.
- Forecast values are displayed on the screen, where DRP will suggest reorder quantities to meet forecasted demand.
Watch the video below to learn more about Distribution Requirements Planning (DRP).
Expediate Return Material Authorisations (RMAs)
Streamline returns and enhance tracking efficiency.
Handling sales returns is a common business task. In the past, this process was often cumbersome without the original invoice number or reference, a scenario that occurred in nearly all cases.
The MYOB Acumatica 2024.1 release simplifies the return material authorization (RMA) process with improved document search capabilities, leveraging details such as sales order type and number, inventory ID, lot or serial number, and order dates.
Users can access a new predefined CR-Return Orders generic inquiry on the Generic Inquiry (SM208000) form. The resulting Return Orders (CR306017) inquiry form displays a list of case-related return orders along with their statuses, as shown below.
The key benefits of this feature include:
- Enhanced employee productivity and customer service: simplifying the creation and tracking of return histories from sales orders. Productivity is boosted by new search criteria that make it easier to locate the original order. Additionally, a new side panel called 'Related Return Documents' has been added for better visibility of all returns linked to an order.
- Improved search functionality: allowing for easy location and updating of returns.
Watch the video below to learn more about Customer Return Improvements.
Picking & Packing Efficiency Improvements
Enhance your picking productivity insights
Previously, wave and batch pick lists were excluded from the Efficiency of Picking and Packing inquiry. With the MYOB Acumatica 2024.1 release, these have now been incorporated, and the inquiry has been refined to include the number of errors and useful operations compared to actual operations. This offers a comprehensive overview of the process for the warehouse manager.
The Efficiency of Picking & Packing Inquiry now includes:
- Wave & Batch Pick Lists.
- Number of actual operations and errors displayed.
- Date and Time Stamps for picking and packing activities.
- The ability to search and filter records by specific parameters such as worksheet or shipment.
The key benefits of this feature include:
- Provides detailed insights into who picked what, when, and their accuracy, with many new fields added.
- Offers a complete audit trail.
- Identifies high performers and those needing assistance to meet their goals.
- Enhances understanding of picking accuracy, speed, and performance.

Bi-Directional Picklists for Paperless Picking
Optimise your time with paperless picking.
Prior to the bi-directional pick-list, customers were limited to less efficient, one-way paths in the warehouse for package picking, restricting them to a single direction to fulfill orders. With the MYOB Acumatica 2024.1 release, customers can now navigate in both directions, speeding up order fulfillment.
This feature enables pickers to gather items in one direction and then guides them in the opposite direction for the next pick list, reducing the number of steps and ensuring the most efficient route through the warehouse.
Users can also find the nearest Pick List when selecting Next List by using a ‘highest to lowest’ and then ‘lowest to highest’ path algorithm. If not, the system defaults to a 'lowest to highest' pattern.
The primary advantages of this feature are:
- Optimally ordered picklists that support bi-directional paths.
- Consolidated quantities for pick lines.
Watch the video below to learn more about Bi-Directional Picklists for Paperless Picking.
Aggregated Quantity at Picking
Enhance efficiency with greater flexibility in picking.
Previously, users couldn't set quantities for picking that would update multiple sales orders simultaneously. However, with the new warehouse management settings and this feature, picker productivity has significantly increased.
This feature accelerates the picking process by consolidating quantities of similar products for multiple sales orders into a single shipment. Users can utilize the Set Qty function to match the total quantity being picked for an item, ensuring this collective quantity is accurately distributed among the sales order lines.
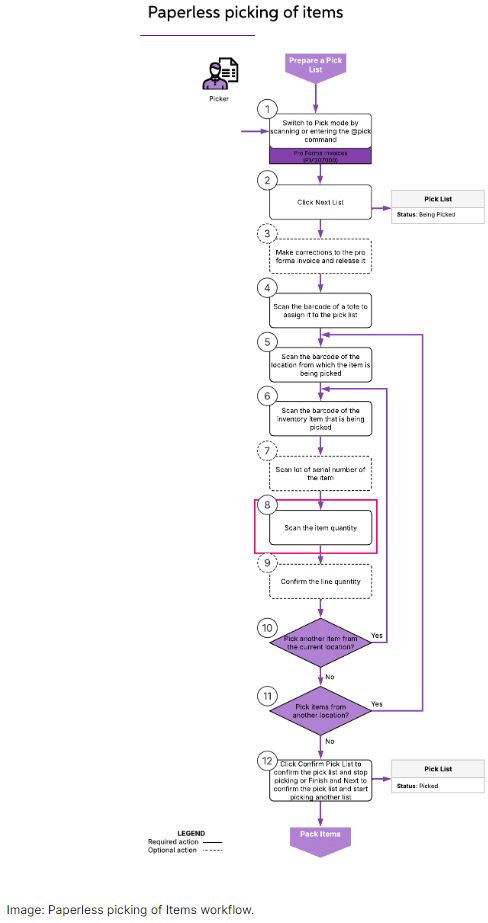
- Accelerated picking of items for multiple sales orders or combined shipments.
The MYOB Acumatica 2024.1 Spring Release brings a suite of powerful tools designed to streamline and enhance your supply chain management. From the advanced capabilities of Distribution Requirements Planning (DRP) to the efficiency improvements in picking and packing, these features are crafted to optimise your operations, reduce manual effort, and improve overall productivity. By leveraging these innovations, your business can achieve greater accuracy, speed, and flexibility in managing inventory and returns. Stay ahead of the curve by integrating these enhancements into your workflow and experience the transformative impact on your supply chain processes.
For a deeper dive into how these updates can benefit your specific operations, explore our other blogs covering Finance, Sales and Customer Management, Project Management, Supply Chain Management, Production, Field Services, and Platform Enhancements.
Additionally, you can access the full release notes here for a complete overview of all the new features and improvements.
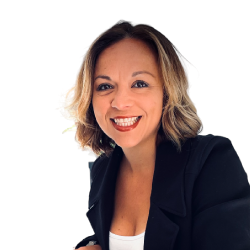