MYOB has introduced a remarkable suite of new features in the 2024.1 Spring Release. This blog will delve into the latest enhancements and functionalities for the MYOB Acumatica Manufacturing Edition.
Enhance demand planning precision with the new capability to clear all Inventory Planning settings for Inactive Warehouses.
Previously, customers had to manually exclude inactive warehouses from Material Requirements Planning (MRP) calculations. This often necessitated manual adjustments or overrides of system-generated data to ensure inactive warehouses were omitted from demand and supply calculations. If a warehouse was inactive, users had to ensure it wasn't selected as the default location, which could involve additional checks and manual updates.
Now, when the Active checkbox is cleared on the Warehouses form, all checkboxes in the Inventory Planning Settings section on the Inventory Planning tab are automatically cleared and set to read-only. This gives planners greater control over their demand planning by using a simple switch in the Warehouse record to clear all Inventory Planning settings, effectively 'hiding' the warehouse from MRP visibility.
The key benefits of this feature include:
- Enhanced control over demand planning: through a simple switch at the Warehouse record that clears all Inventory Planning settings.
Example of Feature use in MYOB Acumatica
Excluding inactive warehouses from Material Requirements Planning (MRP) allows users to concentrate solely on active warehouses, streamlining inventory and resource management. This is particularly useful for businesses operating multiple warehouses, as it simplifies the planning process and guarantees that only relevant data is considered.
Enhance planning accuracy by excluding returns and other specific order types from inventory planning calculations.
Many companies prefer that Material Requirements Planning (MRP) or Distribution Requirements Planning (DRP) do not consider expected return items as supply until they have been inspected, as these items could be damaged or defective.
Previously, Production Managers had to manually adjust inventory levels to account for returned items, often creating separate entries for items awaiting inspection or repair to ensure they were not counted as available stock.
The MYOB Acumatica 2024.1 Release introduces a new feature that allows end users to decide if a receipt should be considered valid supply in Inventory Planning.
The key benefits of this feature include:
- Customer Value: Customers now have the flexibility to choose whether returned goods are included or excluded as supply quantities to offset demand quantities calculated by Inventory Planning.
- Inventory Planning Regeneration: Improved logic in Inventory Planning Regeneration to follow the sales order type setting, determining whether to include or exclude receipts from the supply calculation.
Example of Feature use in MYOB Acumatica
Return orders often involve items that need to be inspected or repaired before they can be restocked. Excluding these orders from inventory planning helps maintain a clear distinction between available inventory and items pending inspection, thus preventing overestimation of available stock.
Enhance material demand planning by accurately forecasting both stock and non-stock kit components.
Previously, MYOB Acumatica users faced challenges in planning the stock components required for assembling kits due to limitations in the inventory planning functionality. The inventory planning regeneration process did not account for the demand requirements of kit components when a supply recommendation was made. Consequently, if a stock kit was included in a sales order and lacked sufficient quantity, users were not notified of the additional demand for the necessary components.
To circumvent this, users would create a kit assembly document as soon as a sales order for a kit was generated. However, the absence of an allocation date in the kit assembly document led to incomplete data being passed to the inventory planning regeneration process, which could not accurately determine when supply and demand were expected.
With the MYOB Acumatica 2024.1 release, enhancements to the inventory planning regeneration process and sales forecast functionality have been implemented to resolve these issues. Users can now create Kit Assemblies directly from the Inventory Planning Display and utilize a new “Requested On” date field in the Kit Assembly, which populates the item plan date.
The key benefits of this feature include:
- An improved inventory planning process that drives demand through the kit specification, enabling accurate calculation and planning of the stock components required for kit assembly—addressing a previous gap in MRP.
Example of Feature use in MYOB Acumatica
Consider a stock kit in manufacturing, such as a "Computer Accessory Kit," which includes the following components:
- Stock Components: Keyboard, Mouse, USB Hub.
- Non-Stock Components: Packaging Box, Assembly Labour.
When the kit is assembled, the individual stock components (keyboard, mouse, USB hub) are deducted from inventory, and the kit itself is added to inventory. The cost of the kit is determined based on the costs of its components at the time of assembly, including the packaging box and assembly labor. When sold, the kit appears as a single line item in the transaction, streamlining the sales process.
Watch the below video to find out more about Inventory Planning for Non-Stock Kits.
Streamline MRP generation with 'planning horizons' that allow organizations to specify time-bound data for inclusion in supply and demand calculations.
Previously, customers with extensive supply and demand data couldn't shorten their planning horizon, necessitating a full MRP run that could take hours to complete.
The MYOB Acumatica 2024.1 release introduces a new MRP time fence feature, enabling planners to define a user-specific planning horizon by days. This results in a significantly shorter and optimized MRP run for short-term planning, eliminating the need for a full MRP regeneration, which can be a much lengthier process.
The key benefits of this feature include:
- Reduced processing times by setting a user-defined planning horizon by days.
- Eliminates the need for a full MRP regeneration, significantly cutting down processing times for customers with extensive supply and demand data.
Only supply and demand plans on or before the regeneration date + number of days specified via Planning Horizon are included in the inventory regeneration process.
Enhanced flexibility for manufacturing workers to report production operations running in parallel.
Previously, in the MYOB Acumatica Manufacturing Edition, reporting quantity completion for production operations out of sequence was not feasible. If a subsequent operation reported a higher completed quantity than a preceding one, this quantity was retroactively applied to the earlier operation.
Manufacturers with nonsequential processes had to depend on shop floor workers to manually document production transactions, such as completed or scrapped quantities, outside of MYOB Acumatica. These transactions then needed to be sequentially entered into the system for each production order, potentially leading to data inaccuracies.
With the MYOB Acumatica 2024.1 release, automatic backward reporting can now be toggled on or off.
The key benefits of this feature include:
- Short cycle times for finished products: workers can avoid wasting time logging out-of-sequence production orders.
- Concurrent operations: for instance, cutting the left and right sleeves of a t-shirt simultaneously.
Example of Feature use in MYOB Acumatica
A user has the ability to cater for real life scenarios where some shop floor workers may be prevented from reporting Operations sequentially due to technology limitations or accessibility issues.
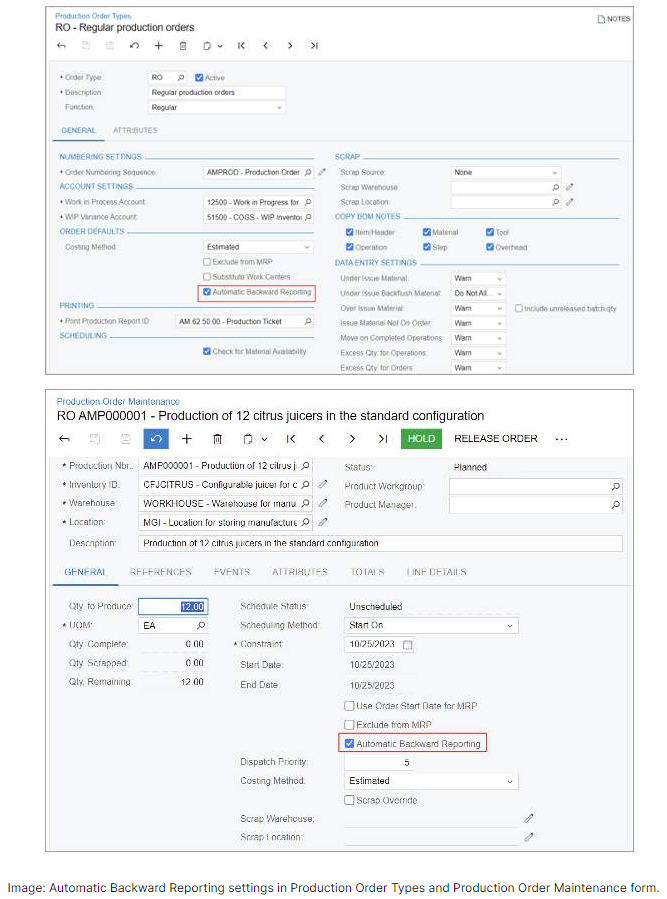
For a deeper dive into how these updates can benefit your specific operations, explore our other blogs covering Finance, Sales and Customer Management, Project Management, Supply Chain Management, Production, Field Services, and Platform Enhancements.
Additionally, you can access the full release notes here for a complete overview of all the new features and improvements.
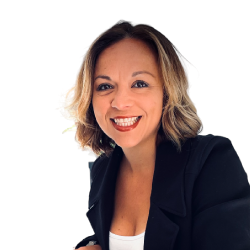