Manufacturing operations just got a boost with the 2024.2 Autumn Release of MYOB Acumatica. This update introduces significant enhancements to production workflows, giving your team more accurate estimating tools, tighter production order linking, and improved visibility into performance. Whether you're managing complex assemblies or custom builds, these new capabilities are designed to help you plan better, execute faster, and stay in control. Let’s dive into what’s new in production.
Enhanced Estimating
The 2024.2 release of MYOB Acumatica has brought notable enhancements to the estimating capabilities. In the past, users had to create multiple estimate revisions to incorporate price breaks, which was a complex process requiring additional solutions. Now, users can develop estimates with different price points based on the number of units a customer plans to purchase, all within a single revision. Price breaks are still optional, allowing users to create estimates without them, as in previous versions of MYOB Acumatica. By incorporating price breaks into estimates, users can accurately represent cost variations due to order quantities and subcontracting expenses, ensuring margins are maintained while offering competitive pricing to customers.
The key benefits of this feature include:
- Competitive Quoting: Facilitates competitive pricing by spreading one-time costs over multiple quantities, enabling users to set pricing and percentage markups for different quantities within a single estimate.
- Price Breaks: Implement distinct pricing strategies based on quantity breaks of the finished goods in the estimate.
- Detailed Cost Management: Assists manufacturers in identifying costs linked to new product launches, ensuring profitability.
A sales engineer may find the new functionality beneficial in the following scenarios:
- When a supplier offers quantity price breaks for purchase parts. The engineer can incorporate these price breaks into the estimate to precisely show how the ordered quantity by the manufacturing customer impacts the cost and margin of the final product.
- When subcontracting costs are a factor. Subcontractor suppliers might impose minimum flat fees for smaller order quantities. By including these price breaks in the estimate, the engineer can accurately determine the increased price and cost of the product, ensuring that margins are preserved despite the additional expenses.
- When the sales engineer aims to offer discounts for order quantities in batch or lot size increments by lowering the markup. By incorporating price breaks into the estimate, the engineer can adjust pricing for various order quantities. This guarantees that customers receive discounts for larger orders while the company continues to meet its margin goals.
The sections below detail the changes that support the enhanced estimating functionality, which is available if the Estimating feature (under the Manufacturing group of features) is enabled on the Enable/Disable Features (CS100000) form.
Changes to the Estimate Form
Image: The Price Breaks tab of the Estimate form.
A new tab called Price Breaks has been introduced to the Estimate (AM303000) form. This tab allows users to add, update, or remove price breaks for primary revisions of estimates that are either New or In Process. The system automatically calculates the cost and price components for each price break and marks the first one added as Primary. This primary price break configuration serves as the reference for order quantity and cost and price components displayed on the Totals tab of the form.
When generating an estimate for a sales quote, the system uses the quantity from the primary price break as the order quantity. By checking boxes in the Print column on the Price Breaks tab, users can choose which price breaks to include in the Sales Quote (CR604500), Quote (SO641000), and Estimate Summary (AM641000) reports. If a user creates a new estimate revision, the system transfers the price breaks from the original estimate revision to the new one, along with any notes and attachments. Similarly, when creating a new estimate using the Create by Copying command from the More menu, the price breaks and their notes and attachments from the source estimate are copied to the new estimate.
An Override check box has been added next to the Overall Markup (%) box on the Totals tab of the Estimate form. Selecting this box allows users to adjust the system-calculated markup percentage for the entire estimate. Users can also select check boxes in the Override Overall Markup (%) column on the Price Breaks tab to manually input the overall markup percentage for individual price breaks.
If a new value is entered in the Overall Markup (%) box on either the Totals or Price Breaks tab, the system recalculates the Total Price and Unit Price using these formulas: Total Price = Total Cost * (1 + Overall Markup % ÷ 100) and Unit Price = Total Price ÷ Order Qty. Additionally, a Round Unit Prices check box has been added to the Summary area of the Estimate form.
When selected, all unit prices on the Totals and Price Breaks tabs are rounded to the nearest whole unit of the respective currency. For instance, $10.49 will round down to $10.00, and $10.50 will round up to $11.00. The Currency box has been relocated from the Totals tab to the Summary area, and all monetary amounts on the form are displayed in the currency specified in this box.
Boxes on the Totals tab of the Estimate form have been renamed, as shown in the following table:
Old Name |
New Name |
Order Qty |
Order Qty. |
Labor Markup Pct |
Labor Markup (%) |
Machine Markup Pct |
Machine Markup (%) |
Material Markup Pct |
Material Markup (%) |
Tool Markup Pct |
Tool Markup (%) |
Overhead Markup Pct |
Overhead Markup (%) |
Subcontract Markup Pct |
Subcontract Markup (%) |
Overall Markup Pct |
Overall Markup (%) |
Boxes in the Summary area and columns on the Operations tab have been renamed, as shown in the following table.
Old Name |
New Name |
Var Labor Cost |
Var. Labour Cost |
Var Overhead Cost |
Var. Overhead Cost |
Fix Labor Cost |
Fixed Labor Cost |
Fix Overhead Cost |
Fixed Overhead Cost |
Changes to the Estimate Summary Report
Image: Price breaks in the Estimate Summary report.
The Estimate Summary (AM641000) report has been enhanced to display the estimate price breaks that have the Print check box selected on the Price Breaks tab of the Estimate (AM303000) form.
The report layout has been updated as follows:
- The Estimate Quantities and Pricing Details section, as shown in the screenshot above, is a new addition. This section provides details on price breaks (when applicable) and includes columns for Item, Description, Lead Time (Days), Qty., UOM, Unit Price, and Extended Price.
- The Estimate Materials section has been reformatted and moved to sit below the Estimate Quantities and Pricing Details section.
- The Quantity column in the Estimate Materials section has been renamed to Qty. per Unit.
- Additionally, the Unit Price and Total Price boxes have been removed from the report footer.
Changes to the Sales Quote and Quote Reports
The Sales Quote (CR604500) and Quote (SO64100) reports have been upgraded to showcase estimate price breaks when the Print check box is selected on the Price Breaks tab of the Estimate (AM303000) form. In the standard system setup, these reports now automatically include estimates, eliminating the need for manufacturers to make additional modifications to incorporate sub-reports with estimate details.
Other Changes
Image: The Price Break check box in the Quick Estimate dialog box.
A new check box labeled Price Break has been introduced in the Quick Estimate dialog box, accessible by clicking the Quick Estimate button on the Estimates tab of the Opportunities (CR304000), Sales Orders (SO301000), and Sales Quotes (CR304500) forms. This check box, which cannot be edited, shows whether the estimate record includes price breaks. If price breaks are present, users can view the details in the dialog box but are unable to alter them for another quick estimate.
Boxes in the Summary area of the Estimate Operation (AM304000) form have been renamed, as shown in the following table.
Old Name |
New Name |
Var Labor Cost |
Var. Labor Cost |
Var Overhead Cost |
Var. Overhead Cost |
Fixed Labor Cost |
Fixed Labor Cost |
Fix Overhead Cost |
Fixed Overhead Cost |
Watch the video below to see a demonstration of Enhanced Estimating.
Enhanced Linking of Production Orders
The MYOB Acumatica 2024.2 release brings transformative improvements to the linking of parent and child production orders. Key advantages of this feature include:
- Enhanced Visibility and Tracking: Empowers manufacturers to evaluate potential delays or impacts on upstream parent production orders with greater precision.
- Streamlined Numbering System: Facilitates easier identification and tracking of production order lineage, ensuring clarity and efficiency.
- Proactive Conflict Alerts: Delivers timely warnings for conflicts with constraint dates within parent-child production orders, including alerts for extending a child’s constraint date beyond the parent’s, helping maintain seamless operations.
Improved Visibility of Related Production Orders
Earlier versions of MYOB Acumatica did not allow for a comprehensive view of all dependencies within a production order. Production managers were required to individually select each material line on the Production Order Details (AM209000) form to view its child orders, a process that was both cumbersome and time-consuming.
Image: The product, parent, and child orders on the Related Production tab.
To resolve this issue, a new Related Production tab has been introduced in the Production Order Maintenance (AM201500) form. This tab provides a consolidated view of the product production order (the top-level order), the immediate parent production order, and the immediate child production orders, along with their respective details. The Related Production tab displays production orders with item plans that are directly linked to the current order or serve as its supply. As a result, if a user cancels or deletes a production order or production material demand, the item plan is removed, and the system updates all associated parent and child relationships. To prevent duplicate information, the Linked Orders section has been eliminated from the References tab of the Production Order Maintenance form.
Enhanced Numbering of Subassembly Orders
With the introduction of MYOB Acumatica 2024.2 users can now configure the system to assign identifiers to the product production order and all its child orders, featuring a common segment and a distinct suffix. This enhancement simplifies the identification of production orders that belong to the same production bill of material (BOM).
Image: The Add Suffix for Production Subassemblies check box.
To enable this feature, the Production Order Types (AM201100) form now includes a new Add Suffix for Production Subassemblies check box located in the General tab under the Numbering Settings section. When this check box is unchecked, the system uses the standard numbering sequence for production order identifiers, as in previous versions. If the check box is checked, identifiers are assigned as follows:
- Common segment generation: The identifier's common segment is derived from the production order numbering sequence and is reduced by four digits.
- Top-level production order: The top-level product production order is assigned the common segment followed by "-000."
- Child production orders: Each child order of the product production order is assigned the common segment followed by a hyphen and a sequential three-digit suffix, starting with immediate child orders and continuing to related orders at each subsequent hierarchy level.
The following diagram illustrates the assignment of identifiers to the related production orders.
Image: Assignment of production order identifiers with suffixes.
To automatically assign suffixes, activate automatic numbering for the production order type. In the Numbering Sequences (CS201000) form, uncheck the Manual Numbering box.
The system assigns the incremental suffix to related production orders when a user generates these orders on the following forms:
- Production Order Maintenance (AM201500)
- Sales Orders (SO301000)
- Inventory Planning Display (AM400000)
- Projects (PM301000) Estimate (AM303000)
- Create Production Orders (AM510000)
- Critical Materials (AM401000)
The system clears the Add Suffix for Production Subassemblies check box by default for all new and existing production order types.
Allocation of a Subassembly as a Material to Another Production Order
MYOB Acumatica 2024.2 now allows the allocation of an existing subassembly as a material to a parent production order.
Image: The Link Prod. Order button.
In the Production Order Details (AM209000) form, a new Link Prod. Order button has been introduced to the table toolbar on the Materials tab. Users can connect a production order's material demand to a subassembly production order if the following criteria are satisfied:
- The production order is either in Planned or On Hold status.
- The Mark for Production check box is selected in the material line.
- The material line is not already linked to a subassembly production order.
- The material line's status is Planned, Released, or In Process.
Upon selecting a material line and clicking the Link Prod. Order button, the system opens the new Production Details dialog box. This dialog box shows production orders for the item specified in the selected material line, provided they have a status of Planned, On Hold, Released, or In Process and are not linked to any other parent production order. When a user selects a subassembly production order in the dialog box and clicks Save, the system changes the allocation type of that production order from Production Supply Prepared to Production for Prod. Prepared on the Inventory Allocation Details (IN402000) form. Additionally, the system updates the product, parent, and child relationships on the Related Production tab of the Production Order Maintenance (AM201500) form for all associated production orders.
Generation of Orders for Subassemblies
Previously in MYOB Acumatica, users could generate subassembly production orders using the Production Order Maintenance (AM201500) and Critical Materials (AM401000) forms. However, this feature was unavailable on other forms used to create production orders.
Now users can generate subassembly production orders on the following forms:
- Create Production Orders (AM510000)
- Sales Orders (SO301000)
- Inventory Planning Display (AM400000)
- Projects (PM301000)
- Estimate (AM303000)
Image: The new check box on the Create Production Orders form.
In the Create Production Orders form, the Selection area now features a Generate Orders for Subassemblies check box. When this option is selected by a user, the system creates a production order for each selected item in the table, including all necessary subassembly production orders.
Image: The Generate Orders for Subassemblies check box.
In the Sales Orders form, the Generate Orders for Subassemblies column is now included in the Production Orders dialog box, accessible by choosing Create Production Orders from the More menu. When the Generate Orders for Subassemblies check box is selected for a sales order line associated with a production order, the system generates a production order for the item and its subassemblies.
In the Inventory Planning Display form, the Create Production Orders dialog box now features the Generate Orders for Subassemblies column, which users can access by selecting Manufacture on the form toolbar. Checking the Generate Orders for Subassemblies box in a row with an item marked for production order creation (indicated by the selected check box) prompts the system to initiate a production order for the item and all necessary subassembly production orders.
In the Projects form, the Generate Orders for Subassemblies check box is now part of the Create Production Orders dialog box, which becomes available when the user clicks Create Prod. Order on the toolbar within the Production Orders tab. When this check box is selected, the system generates a production order for the specified inventory item, along with all required subassembly production orders.
In the Estimate form, the Generate Orders for Subassemblies check box has been added to the Create Production Order dialog box, which opens when a user clicks Create Production Order on the More menu. Selecting this check box prompts the system to create a production order for the estimate, including all necessary subassembly production orders.
In previous versions of MYOB Acumatica, users could create subassemblies by selecting Generate Orders for Subassemblies from the More menu within the Production Order Maintenance form. The system would then generate a production order for each material line, provided the following criteria were met for the stock item on the Manufacturing tab of either the Item Warehouse Details (IN204500) or Stock Items (IN202500) form:
- The system specified the Default BOM ID.
- The replenishment source was designated as Manufacturing.
The system checks the Mark for Production status on the Production Order Details (AM209000) form and generates a subassembly production order only if selected.
The system automatically selects the Mark for Production check box for a material line if the stock item in the line has Production chosen in the Dflt Mark For box on the Manufacturing tab of the Stock Items form.
Enhancements in Finite Production Scheduling
The modifications outlined in this section are relevant for companies that have activated the MYOB Acumatica Planning and Scheduling feature on the Enable/Disable Features (CS100000) form and are utilising this capability. When a finished product is intended for sale and includes at least one custom-engineered subassembly, production should be organised to ensure all dependent components are completed before the final assembly.
The MYOB Acumatica 2024.2 update has refined the finite scheduling logic. The system now considers the constraints of related production orders, as well as the availability of work centers and machinery. For example, when scheduling a parent production order along with its child production orders on the Rough Cut Planning (AM501000) form, the system sequences the child production orders to ensure they are completed in time for the parent production order.
Previously, users might have encountered unexpected results when scheduling a production order on the Rough-Cutut Planning and Production Order Maintenance (AM201500) forms, particularly if the system calculated a start date in the past. In such cases, the system would automatically reschedule the production order by changing its Scheduling Method to Start On and updating its Constraint Date to the current date. Now, the system avoids automatically adjusting the constraint date and scheduling method for a product production order or individually scheduled child production orders. Instead, if a user sets the Scheduling Method to Finish On and the system calculates a start date in the past, a notification is provided.
Additionally, the system issues alerts if altering the constraint date of a parent or child production order could disrupt the timely production of subassemblies required to fulfill the parent order's demand.
Other Improvements
In the Production Order Maintenance (AM2015PL) list of records and on the Material Wizard (AM300010) form, the following columns have been renamed for improved clarity:
- Product Order to Product Production Nbr.
- Parent Order to Parent Production Nbr.
The Product Order Type, Product Production Nbr., Parent Order Type, and Parent Production Nbr. columns are now displayed on the following forms:
- Release Production Orders (AM500000)
- Close Production Orders (AM506000)
- Print Production Orders (AM511000)
- Rough Cut Planning (AM501000)
- Lock Production Orders (AM517000)
- Transactions by Production Order (AM000011)
- Production Summary (AM000006)
- Production Order Maintenance(AM2015PL)
The same columns are also displayed in the lookup table for the Production Nbr. box on multiple forms.
The system now displays confirmation dialog boxes when a user does the following on the Production Order Maintenance (AM201500) and Production Order Details (AM209000) forms:
- Deletes or cancels a production order that has child production orders.
- Removes material demand linked to another production order.
- Deletes an operation whose materials are linked to other production orders.
Understanding Feature Use in MYOB Acumatica: Autumn Release 2024.2
As a production manager, you can link related production to more easily assess potential delays or impacts on upstream parent production orders. This improves scheduling and planning, providing greater predictability and dependency within production plans.
Watch the video below to see a demonstration of Enhanced Linking of Production Orders.
Enhancements to the Production Order Performance Report
MYOB Acumatica 2024.2 has enhanced this report to incorporate more detailed information, including labour hours, costs, overhead by operation, and all transactions related to materials and labour. This enhanced information grants users comprehensive access to all pertinent data in a single, consolidated view, facilitating more detailed reviews and simplifying the investigation of anomalies.
Changes to the Report Layout
Starting in MYOB Acumatica 2024.2 depending on the selected report parameters and data availability, the layout of the Production Order Performance (AM652000) report may include new sections. Each section is shown in the screenshot below its description.
Operations: Provides users with a view of the planned and actual production hours and labour cost by operation.
Image: The Operations section.
Subcontracts: Displays the subcontracting details related to the production order.
Image: The Subcontracts section.
Materials: Shows the details of materials related to the production order.
Image: The Materials section.
Subcontract Transactions: Educates users on the subcontract transactions associated with the production order.
Image: The Subcontract Transactions section.
Material Transaction: Provides data on the material transactions related to the production order.
Image: The Material Transactions section.
Operation Transactions: Shows the operation transactions related to the production order.
Image: The Operation Transactions section.
Sales Order Production Totals: Shows the costs of the production order that are linked to sales order demand.
Image: The Sales Order Production Totals section.
Changes to the Report Parameters
On the Production Order Performance (AM652000) report form, the Report Parameters tab has been enhanced as follows (see the screenshot below):
- The Order Type parameter has been renamed to Prod. Order Type.
- The Include Production Transaction Details check box has been added after the Production Nbr. parameter. Selecting the check box adds the Subcontract Transactions, Material Transaction, and Operation Transactions sections to the resulting report. The check box is cleared by default.
- The Sales Order Type and Sales Order Nbr. parameters have been added. By specifying these parameters, users can generate reports by sales order demand and review the costs of the entire production order.
Image: The Report Parameters tab of the report form.
A New Command
The Production Order Performance command is now accessible in the More menu of the Production Order Maintenance (AM201500) and Production Order Details (AM209000) forms. Selecting this command allows users to produce the Production Order Performance (AM652000) report for the active production order.
These new production features bring better visibility and flexibility to your manufacturing operations—helping you stay on schedule, reduce waste, and improve overall performance. With enhanced estimation and tighter production linking, you can move from planning to production with ease.
Interested in how these updates could transform your production workflows? Reach out to us to explore the possibilities with MYOB Acumatica 2024.2.
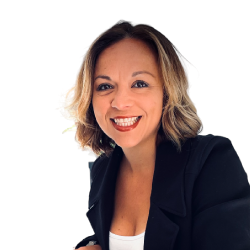