In the fast-paced world of manufacturing, quality is everything. A single defect can lead to costly product recalls, wasted materials, regulatory fines, and even long-term damage to a company’s reputation. Yet, many manufacturers still struggle with quality control, often due to outdated systems, inconsistent processes, and lack of real-time data.
The good news? MYOB Acumatica ERP offers a modern, cloud-based solution that helps manufacturers streamline quality control, ensuring that every product meets high standards before it reaches the customer. In this blog, we’ll explore how MYOB Acumatica helps businesses tackle common quality control challenges and improve overall manufacturing efficiency.
Why Quality Control is Critical in Manufacturing
Manufacturers must maintain strict quality standards to ensure:
- Customer Satisfaction – Delivering reliable, high-performing products builds trust and brand loyalty.
- Regulatory Compliance – Many industries, such as food, pharmaceuticals, and automotive, must adhere to strict quality regulations.
- Reduced Costs & Waste – Poor quality leads to rework, scrap, and inefficiencies that impact profitability.
- Stronger Reputation – Inconsistent quality can hurt your brand and cost future business.
Despite its importance, quality control remains a major challenge due to manual inspections, disconnected data systems, and difficulty tracing defects back to their source.
How MYOB Acumatica ERP Solves Quality Control Challenges
MYOB Acumatica ERP provides a fully integrated, cloud-based solution designed to eliminate inefficiencies and help manufacturers achieve consistent, high-quality production. Here’s how:
1. Real-Time Quality Monitoring & Analytics
MYOB Acumatica delivers real-time visibility into production quality, allowing teams to detect potential defects early before they escalate. With advanced dashboards and reporting tools, manufacturers can track trends, spot inconsistencies, and make data-driven decisions to enhance product quality.
🔹 Benefit: Proactive quality monitoring reduces defects and prevents costly product recalls.
2. Standardised Quality Control Processes
Many manufacturers struggle with inconsistent quality inspections across different batches. MYOB Acumatica solves this by enabling businesses to create standardised testing protocols, quality checklists, and inspection workflows, ensuring that every product meets the same high standard.
🔹 Benefit: Consistent, repeatable quality processes eliminate variability and improve reliability.
3. Advanced Lot Tracking & Full Traceability
When quality issues arise, manufacturers need to quickly identify the root cause—whether it's a specific raw material, machine, or supplier. MYOB Acumatica’s lot and serial tracking capabilities provide full visibility into materials and production history, making it easier to track defects and prevent recurring issues.
🔹 Benefit: Faster problem resolution, reduced downtime, and improved supplier accountability.
4. Automated Quality Inspections
Instead of relying on manual inspections (which are prone to human error), MYOB Acumatica automates quality checks at key stages of production. This means that quality control happens seamlessly within the workflow, ensuring that no product leaves the factory without meeting standards.
🔹 Benefit: Increased accuracy, reduced inspection time, and lower defect rates.
5. Simplified Regulatory Compliance
For industries with strict quality regulations, compliance can be a time-consuming challenge. MYOB Acumatica automates compliance tracking, maintains detailed audit trails, and generates reports for regulatory audits, ensuring businesses meet industry standards effortlessly.
🔹 Benefit: Reduced risk of fines, legal issues, and compliance failures.
6. Continuous Improvement with Integrated Feedback Loops
Quality control isn’t just about catching defects—it’s about preventing them from happening in the first place. MYOB Acumatica enables manufacturers to create real-time feedback loops between quality control and production teams. If an issue arises, corrective actions can be implemented immediately, ensuring continuous improvement over time.
🔹 Benefit: Fewer recurring defects and a culture of quality excellence.
Why MYOB Acumatica ERP is a Game-Changer for Manufacturers
With powerful automation, real-time analytics, and seamless integration across operations, MYOB Acumatica ERP takes quality control to the next level. Manufacturers can:
✔ Reduce waste & rework by catching defects early.
✔ Increase efficiency with automated workflows and inspections.
✔ Improve traceability to quickly resolve quality issues.
✔ Meet industry standards without the compliance headache.
✔ Enhance customer satisfaction by delivering consistently high-quality products.
MYOB Acumatica unites your manufacturing and distribution teams, processes, and data in one
place, helping you control product quality and mitigate any issues.
Integrate quality management across every facet of your business from accounting and purchasing, to manufacturing and distribution. Centralising your processes will increase traceability, reduce compliance risks, improve customer satisfaction, and automate time consuming manual tasks.
MYOB Acumatica integrated quality management features and benefits
Quality Testing | Perform end-to-end QC testing for incoming raw materials, production, purchasing, inventory, and shipping. |
Checkpoints and inspections | Execute inspection plans, checklists, and QC tests against products, people, and equipment. |
Certificate of Analysis (COA) | Generate COA and production deviation documents and reports. |
NC & CAPA | Track non-conformances, maintain a complete audit trail, and manage corrective and preventive action processes. |
AQL & Sampling | Carry out 100% inspection or sampling routines (AQL and non-AQL). |
Traceability and Recall Notices | Implement forward and backward tracing of all movements of a serial or lot number. |
Packaging Bills of Material | Assign QC tests to sub-assemblies and finished goods that are executed and validated during production. |
Lot-Based Quality Control | Perform quality control testing based on individual lots. |
Mobile Data Collection | Conduct QC and capture data from any location via mobile and web. |
Reporting & Analytics | Report with user-friendly and pre-built reports for vendor, production, and stability analytics. |
Education & Training | Manage the training process and keep employee and training records organised, up-to-date, and compliant. |
Supplier/Vendor Management | Evaluate, score, and summarise the activity and performance of your suppliers/vendors. |
Audit Management | Support the complete audit from beginning to end in compliance with corporate standards and industry regulations. |
Health & Safety | Store, manage, and access required health and safety records. |
Ready to Improve Your Manufacturing Quality?
At Avanza Solutions, we specialise in helping manufacturers implement MYOB Acumatica, ensuring they get the most out of their ERP investment. Let’s talk about how we can help you streamline quality control and drive efficiency!
Contact us today to learn more.
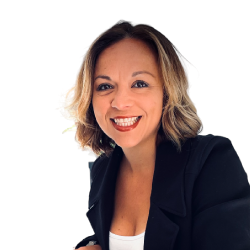